Featured in: asdfsafs sss
Our roadmap
Video on Vimeo
By playing the video you accept the privacy policy of YouTube (third-party provider). More information in our privacy policy.
Video on Vimeo
By playing the video you accept the privacy policy of YouTube (third-party provider). More information in our privacy policy.
February 2024
Solar tower
Synhelion has completed the construction of the solar tower. The tower of DAWN is about 20 meters high, and it houses our key innovations to produce solar fuel: the receiver, the reactor, and the thermal energy storage. The tower is uniquely configured to facilitate efficient fuel production. Positioned facing north, its design minimizes shadow casting on the mirror field.
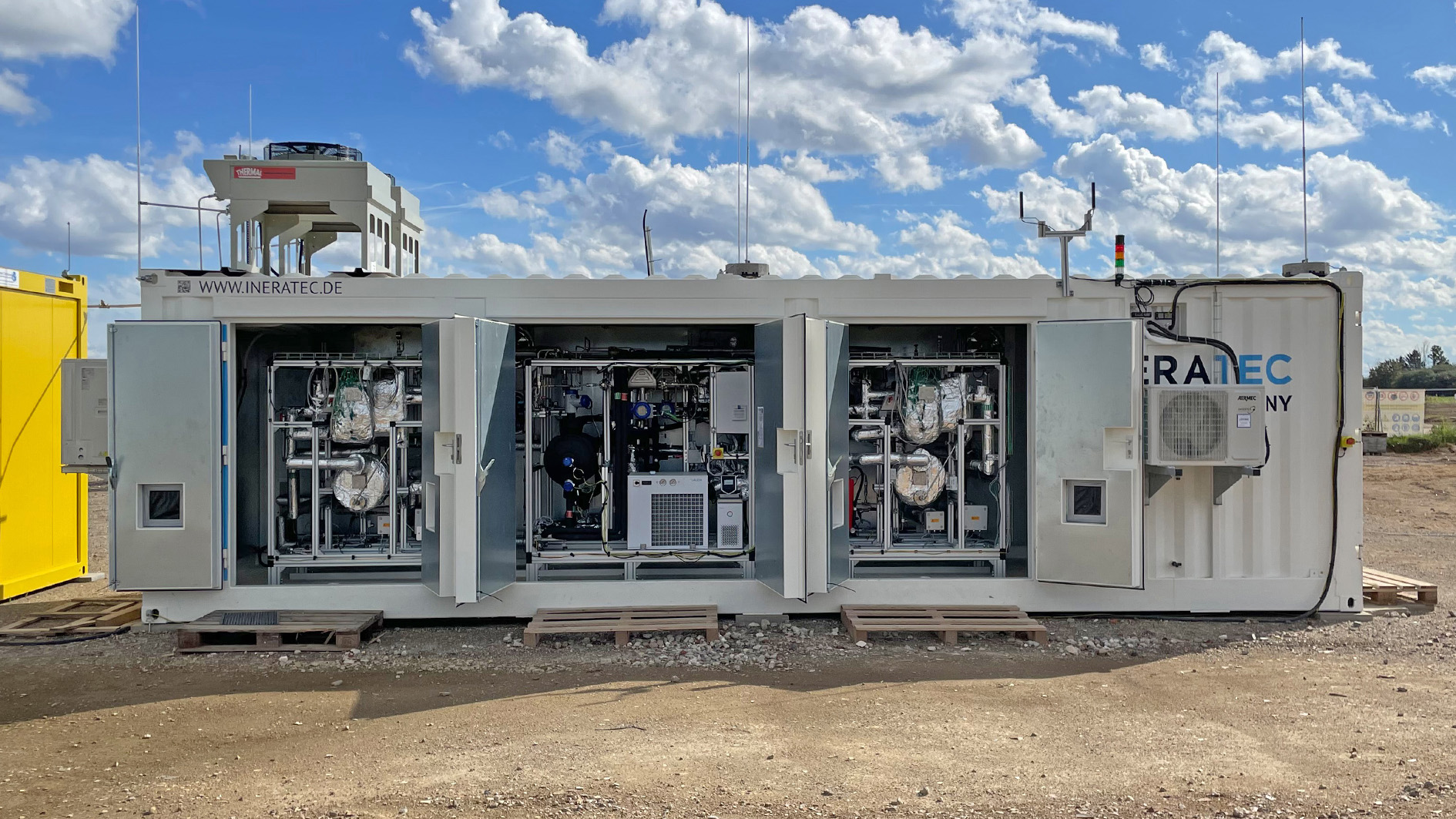
March 2024
Fischer-Tropsch plant
The Fischer-Tropsch unit has been delivered to the plant DAWN site. This facility plays a crucial role in converting sustainably produced syngas, the universal key to renewable liquid fuel, into synthetic crude oil (also called syncrude). Following this conversion, the syncrude undergoes additional refinement in a refinery to yield jet fuel, diesel, or gasoline.
jhgjgjhgkjhgjkhgjkhg |
jhgjkhgjhkgkhjgjkhgjlhg |
kjhkjhkjlhjkhjhkjlh |
jkhgjhjkniuhjhg zgjzhgjk gkhj g gjh gj gjkg j gu glug g ug uzg luzg.
hjk hj hjh ljh jlh jlh ljkh jlkh ljk hkj hjkl hljkh jlk hjk hjk hlkjhkljhkjlhljkhjkhkjhkjkjhjkh kjh jh hjh jkhjkh k hh jhjkhkj lh jkhljk ljkhjk h
Why solar fuels?
Compatible.
Solar fuels are chemically akin to fossil fuels. They are fully compatible with the global fuel infrastructure. There is no need to adapt or refit combustion engines, refineries, fuel distribution, or filling stations.
Affordable.
Solar fuels are an economically viable substitute for fossil fuels. Our technology is affordable thanks to a much higher energy conversion efficiency than other synthetic fuel technologies.
Versatile.
Jet fuel for planes, gasoline for cars, marine fuel for ships, and diesel for trucks – Synhelion technology yields any type of fuel. Solar fuels can replace fossil fuels in all application areas.
Scalable.
Solar fuels are scalable to cover global fuel demand. Thanks to the grid-independent setup of our plants, the technology can scale quickly and independently.
Eco-friendly.
The entire life cycle of solar fuels is based on environmentally-friendly principles. The fuels are produced with renewable energy and emit not only less CO2 but also less noxious gases than conventional fuels.
Storable.
Liquid fuels have a very high energy density. They can be transported and stored for a long time without compromising their quality. A winning combination of two non-negotiables for many fuel-consuming industries.
Independent.
Ideal conditions to produce solar fuels can be found on any continent. The independence from fossil resources results in greater autonomy. Shorter transportation routes are another key asset.
Carbon-neutral.
Our solar fuels close the fuel carbon cycle. They only release as much CO2 into the atmosphere as was used for their production.